ZERO DOWNTIME – Wie die vorausschauende Wartung die Automobilfertigung revolutioniert
Richard Habering | 14. Juli 2021
In der Automobilproduktion stehen die Bänder niemals still. Im Durchschnitt läuft alle 14 Sekunden ein Motor von den Montagebändern – in Spitzenzeiten werden sogar über 6.000 Motoren pro Arbeitstag produziert. Zudem besteht in der Automobilindustrie ein extrem hoher Anspruch an die Präzision der Anlagen. Die verschiedenen Produktionsstationen sind im eingeschwungenen Zustand optimal aufeinander abgestimmt. Ein Schaden hat Auswirkungen auf die ganze Produktionsstraße. Um ungeplante Ausfälle und Anlagenstillstände zu vermeiden, setzt man daher bereits in vielen nationalen und internationalen Automobilwerken auf moderne Instandhaltungskonzepte mit vorausschauender Wartung.
Speziell im Karosseriebau sind die Prozessabläufe sind fließend. Steht ein Maschinenteil still, fällt die komplette Produktionslinie aus. Um die elektrischen Leitungen und Zufuhrpakete der Roboter in der rotierenden Bewegung sowie der Linearbewegung auf der 7. Achse ständig im Blick zu haben, hat igus seine Condition-Monitoring-Lösung i.Sense entwickelt. Sie informiert jederzeit über den aktuellen Betriebszustand, erkennt Unregelmäßgkeiten sofort und verhindert damit proaktiv unnötige Maschinenstillstände.
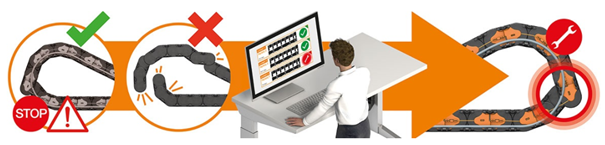
Generell bedeutet Condition Monitoring (oder auch Zustandsüberwachung) die regelmäßige oder permanenten Erfassung des Maschinenzustandes, z. B. des Verschleiß. Zwei Ziele werden dabei verfolgt: Sicherheit und Maschineneffizienz. Werden smart plastics zur Zustandsüberwachung genutzt, melden sie sofort den Eintritt unerwarteter Betriebszustände, schalten ab oder geben Alarm. Automobil Fertiger minimieren auf diesem Weg Anlagenausfälle und Stillstandszeiten:
- Erfasst regelmäßig oder permanent den Maschinenzustand
- Vermeidet Crashs durch schnelles Abschalten
- Datenaufzeichnung über i.Sense Module
- Einfache und effizinete Inbetriebnehme bzw. Retro-Fitting bestehender Anlagen
Auf i.Sense folgt i.Cee – die Lösung zur vorausschauenden Wartung in der Automobilfertigung
In der Fertigungslinie für den Antriebsstrang besteht ein hoher Anspruch an die Zuverlässigkeit der Maschinen. Die verschiedenen Stationen mit teils langen Wegen bilden ein komplexes System mit hoher Dynamik, ein Schaden hat Auswirkungen auf die ganze Produktionsstraße. Im besten Fall läuft die Produktion ohne Störungen durch und Stillstände können mit Hilfe von i.Cee, der Predictive Maintenance Lösung von smart plastics, sinnvoll geplant werden.
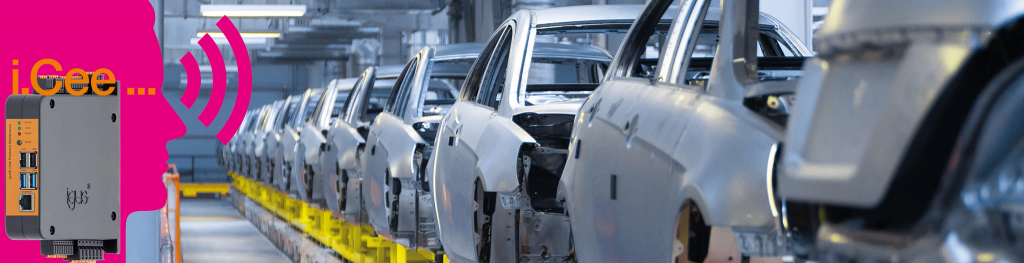
Das zentrale Element im Bereich der vorausschauenden Wartung stellt die i.Cee Software dar. Sie macht, in Verbindung mit Sensoren an der Energieführungskette, der Gleitlagerbuchse oder einem Linearschlitten, die Produkte zu smarten Produkten. Dieses Upgrade schafft die Möglichkeit, die maximale Lebensdauer der igus Produkte zu ermitteln und den perfekten Servicezeitpunkt anzugeben. Mit der von uns gestellten Software und wenigen Sensoren werden also aus den Standardprodukten im Handumdrehen eine smarte Energieführung oder Lagertechnik:
- Teure Produktionsausfälle vermeiden
- Voraussage punktgenauer Wartungen
- Nutzung der maximalen Lebensdauer der eingesetzten Komponenten
- Ein einfacher Schritt zur Integration Ihrer Anlage(n) in vernetzte Industrie 4.0 Konzepte
In der Endmontage gibt es den letzten Schliff in der Fertigungskette. Der Anspruch an störungsfreie Abläufe ist hier aber nicht weniger gering als zu Beginn der Produktion. Manipulatoren, die in diesem Schritt oft Menschen bei der Fertigung unterstützen, sollten leicht zu bewegen sein. Hier sind Energieketten aus Kunststoff, leicht aber robust, genau richtig. Mit unterstützenden Rollen können hier auch lange Wege stetig und verlässlich verfahren werden.
Best Practices der OEMs zeigen eindrucksvoll die Vorteile der vorausschauenden Wartung
Ein Praxisbeispiel eines renommierten OEMs aus Süddeutschland: Die Energiekette eines Roboters wurde bis dato auf Sicht durch einen Wartungsmonteur geprüft. Der Roboter hat sechs Freiheitsgrade und arbeitet 24 h an 7 Tagen die Woche. Ohne smarte Technik wurde die Kette bisher alle 3 Monate auf Verschleiß untersucht und bei Bedarf – also erkennbaren Beeinträchtigungen – gewechselt. Oftmals kam es schon innerhalb dieser Zyklen dennoch zum Bruch, weil die Maschinenprogrammierer minimale Änderungen vorgenommen hatten oder weil minimale Schäden mit dem bloßen Auge nicht erkannt wurden. Teilweise ist auch über viele Monate hinweg gar nichts passiert, dafür aber im Folgequartal gleich zweimal. Verschleiß und Defekte an Bauteilen sind von einer solchen Vielzahl äußerer Einflüsse abhängig, dass sich verlässliche Prognosen kaum ableiten lassen – gerade in solch hochkomplexen Produktionsumgebungen wie in der Automobilfertigung. Mit smart plastics i.Cee lässt sich die vorausschauende Wartung in der Automobilfertigung in wenigen Schritten einführen.