Welche Vorteile hat die Optimierung einer bewegten Anwendung?
igu-blog-adm | 8. August 2019
Geberkabel und Motorkabel werden, dem Bauraum geschuldet, in der Industrie meist parallel zueinander verlegt. Sie kommen aus demselben Schaltschrank, durchlaufen denselben Kabelkanal, bewegen sich zusammen durch dieselbe Energiekette und werden schließlich an den nebeneinander liegenden Anschlüssen des Motors befestigt. Die gegenseitige Signalbeeinflussung, wenn Netzwerk-, Encoder- oder Servosignale nebeneinander verlaufen, ist häufig nicht leicht abzuschätzen.
Der Startimpuls des Motors (Anlaufstrom), wie auch die Leitungslänge der Verbindungskabel oder etwaige Umgebungsbedingungen (wie z.B. ein Schachtofen in der Nähe, eine Schweißzelle, ein Frequenzumrichter oder andere Störquellen) haben entscheidenden Einfluss.
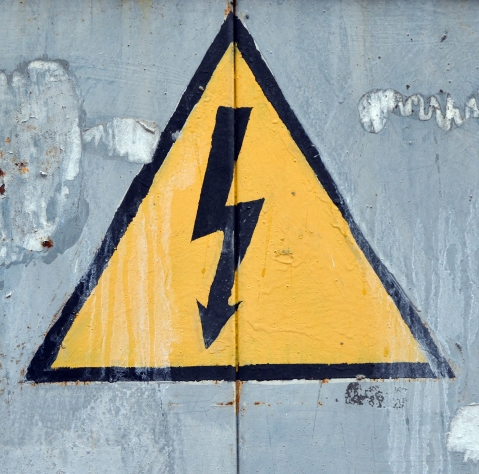
Zusätzlich erhöht jede Schnittstelle das Risiko, dass die Anlage durch Störsignale von außen beeinflusst wird. Oftmals sind Zwischensteckungen, die beispielsweise über Sockel- und Tüllengehäuse auf Bleche geschraubt sind, nicht zu vermeiden. Insbesondere wenn eine Maschine umgebaut wird oder sich im Bauprozess Änderungen ergeben und die Leitung verlängert werden muss, gibt es viele Anwender, die statt eines Verlängerungskabels mit Stift- und Buchsenkontakten ein ganz neues und von der Länge her passendes Kabel verwenden.
Die Zwischenstecker bieten jedoch einen Vorteil für das Handling der einzelnen Baugruppen, können sich aber auch – und vor allem bei schlechter Verarbeitung – negativ auf die Maschine auswirken. Durch Steckerplatten, die gut in die Anlage eingeplant werden, kann die gesamte Maschine in gut zu handhabende Baugruppen gesplittet werden. Durch diese Baugruppen wird Ihr System modular. Komponenten werden durch wenige Handgriffe austauschbar.
Vorteile der Optimierung einer bewegten Anwendung
Überwiegen die Vorteile der Modularität in Baugruppen die Risiken durch elektromagnetische Störungen?
Es gibt mittlerweile verschiedenste Lösungen, um eine Baugruppe modular vom Handling aber auch prozesssicher in der Anwendung zu machen. In diesem Beitrag möchten wir Ihnen eine Lösung vorstellen, die zusätzlich zu den oben genannten Vorteilen eine klare Kodierung der Elemente erlaubt, um eine Verstecksicherheit für z.B. ungeschultes Personal, enge Bauräume oder schlechte Lichtverhältnisse sicherzustellen.
Stillstandszeiten reduzieren, Handling vereinfachen, Prozess optimieren
Am Beispiel für eine automatische Produktionslinie erklärt:
Alle Verbindungskabel sowie weitere bewegliche Teile, wie z.B. die Energieführungskette, können mit individuell auf die Anwendung abgestimmten Modulsteckverbindern optimiert werden. Dies ermöglicht eine definierte und einfach zu handhabende Schnittstelle, die den Austausch einer Baugruppe sicherstellt.
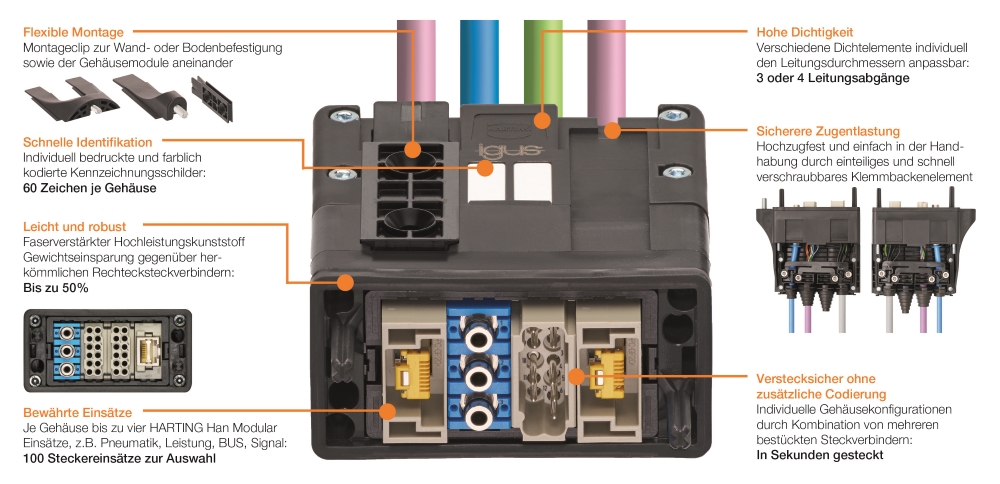
Mehrarbeit reduzieren
Z.B. für Einzelfertiger oder Sondermaschinenbauer:
Im Normalfall wird der Schaltschrank in einer gewissen Entfernung zum Feld, in dem sich die Motoren, Geber, Sensoren, Lichtschranken, Sicherheitskontakte sowie Not-Aus-Schalter befinden, aufgestellt.
Vor der Inbetriebnahme (IBN) beim Endkunden wird jede Anlage bei dem Hersteller aufgebaut, parametriert und getestet. Das heißt, dass alle Komponenten entsprechend der Spezifikation miteinander verbunden werden. Nach der erfolgreichen Endkontrolle wird die Anlage in einige Grundmodule zerlegt und für den Transport verpackt. Da der Transportweg oder die Verpackungsmöglichkeiten hier maßgebend sind, wird die endgetestete Anlage entsprechend demontiert. Bei dem Endkunden vor Ort in der Produktion werden die einzelnen Teile an ihren Bestimmungsort gebracht und erneut verkabelt. Die IBN-Techniker verbringen oft mehrere Tage damit, die Anlage der Dokumentation entsprechend erneut aufzubauen und anzuschließen. Dabei können Fehler auftreten, welche umständlich gesucht und behoben werden müssen.
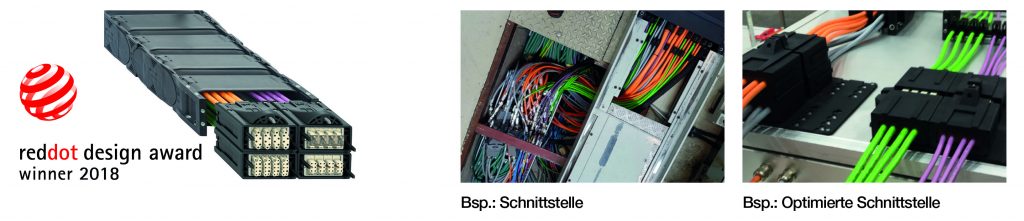
Hochoptimierte Schnittstellen vereinfachen Ihr Baukastensystem
Einfache Wartung, sichere Funktion
Z.B. für Werkzeugmaschinen:
Hochzyklische und schnelle Anwendungen, wie sie typischerweise in einer Werkzeugmaschine gefordert sind, profitieren hier ebenfalls von einer modular ausgelegten Baugruppe. Elektroleitungen und Hydraulikschläuche werden in einem Mehrachssystem verwendet, welches dann als Baugruppe in die jeweilige Maschine eingebaut wird. Hier sind aufeinander abgestimmte Materialien und Komponenten nötig, um eine reibungslose Produktion sowie hohe Standzeit und eine lange Lebensdauer zu sichern.
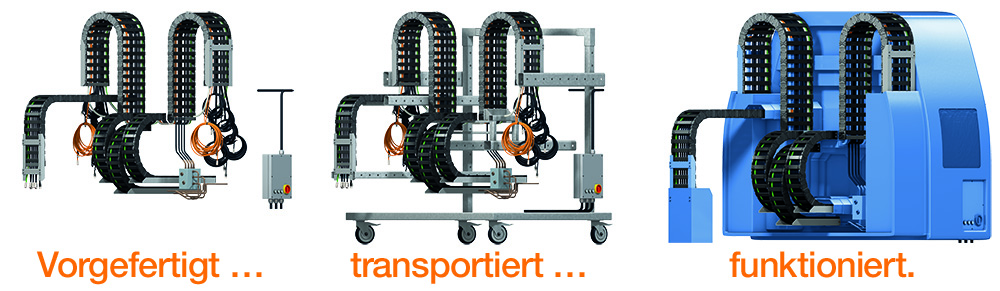
Die oben genannten Beispiele sollen Ihnen Möglichkeiten für Ihre Prozessoptimierung aufzeigen. Falls Ihr Interesse geweckt ist und Sie Bedarf an einer persönlichen Beratung haben, so stehen Ihnen die Projektmanager von igus® jederzeit zur Verfügung. Wir beraten Sie individuell über modulare Steckverbinder (Module Connect) oder schnittstellenoptimierte Energieführungssysteme (readychain® Standard oder Standard+).
Gerne informieren wir Sie auch über einbaufertige Energieführungsketten auf Transportgestellen (readychain® Premium auf readychain® rack), welche direkt an definierten Befestigungspunkten in Ihrer Maschine verbaut werden können.