Beschichtungen für Wellen: Nitrieren oder Verzinken?
Lars Butenschön | 30. April 2020
So wie es eine schier unendliche Zahl von verschiedenen Gleitlager-Lösungen gibt, gibt es auch nicht weniger verschiedene Ausführungen von dazu passenden – oder unpassenden – Werkstoffen für Wellen. Tatsächlich können unterschiedliche Wellenwerkstoffe und deren Beschichtungen für völlig unterschiedliche Verschleißbilder mit dem selben Gleitlager liefern. In diesem Blogpost will ich einmal auf zwei häufig verwendete Beschichtungen für Wellen eingehen und die Frage beleuchten: Welche Beschichtungen für Wellen eignen sich besser für Gleitlager aus Kunststoff: Nitriert oder verzinkt?
Galvanische Verzinkung von Wellen
Bei der galvanischen Verzinkung werden die Werkstücke nicht in eine Zinkschmelze, sondern in einen Zinkelektrolyten eingetaucht. Dabei wird das zu verzinkende Werkstück als Kathode in die Lösung gehängt. Als Anode benutzt man eine Elektrode aus möglichst reinem Zink. Beim galvanischen Verzinken ist der Zinkauftrag proportional zu der Stärke und Zeitdauer des Stromflusses, wobei – abhängig von der Werkstückgeometrie – eine Schichtdickenverteilung über das gesamte Werkstück entsteht. Dieses Verzinkungsverfahren hat eine Reihe von Vorteilen.
Es schafft reine, einheitliche und daher sehr korrosionsbeständige und gut chromatierbare Überzüge. Die Schichtdicken sind genau einstellbar und sorgen somit für Metallersparnis. Es besteht keine Notwendigkeit des Nacharbeitens von Gewinden, Passstellen, etc. Eine Hitzeeinwirkung auf das Grundmaterial tritt nicht ein, so dass es auch nicht zu Verformungen kommt. Der eigentliche Korrosionsschutz entsteht beim galvanischen Verzinken durch die Passivierung der Zinkschicht. In Bezug auf die Auswirkungen der galvanischen Verzinkung auf die speziellen Anforderungen der Wellen-Buchsen- Verbindung und den Wellenverschleiß überwiegen die negativen Effekte.
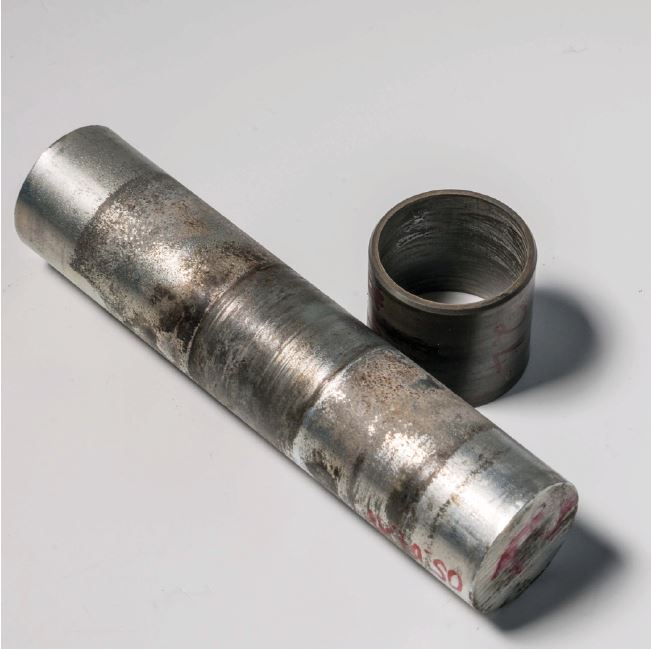
Der eigentliche Überzug einer galvanisch verzinkten Welle ist relativ weich. Zudem entsteht durch die Passivierung der Schicht („Weißrost“) eine vergleichsweise raue Oberfläche. Es findet relativ schnell ein Abtrag der schützenden Schicht statt, wodurch im Kontaktbereich des Lagers der Korrosionsschutz verloren geht. Gleichzeitig steigt der Reibwert an. Dabei spielt es keine Rolle, ob metallische oder Kunststoffgleitlager eingesetzt werden. In den meisten Anwendungen kann der Korrosionsschutz nur aufrecht erhalten werden, wenn die Lagerstelle mit Fett versorgt wird.
Nitrierung: Gasnitrierung und Nitrocarburierung
Auch beim Nitrieren werden zwei Methoden unterschieden,
die Gasnitrierung und die Nitrocarburierung. Beim Gasnitrieren diffundiert in einer aufgespaltenen Ammoniak-Gasatmosphäre Stickstoff in die Bauteile ein, üblicherweise bei 500 – 530 °C. Durch lange Behandlungszeiten von 10 – 160 Stunden werden Nitrierhärte-Tiefen (Nht) von 0,1 – 0,9 mm erzielt, je nach verwendetem Werkstoff. Hauptziele sind die Verbesserungen der Bauteilfestigkeit, der Verschleißfestigkeit, der Gleiteigenschaften, der Temperaturbeständigkeit und der Biegewechselfestigkeit. Die Gasnitrierung erlaubt zudem eine partielle
Behandlung des Werkstoffes.
Bei der Nitrocarburierung wird bei 560 – 580 °C eine Nitrocarburier-behandlung durchgeführt. Neben Stickstoff diffundiert auch Kohlenstoff in das Material. Die Behandlungszeit beträgt üblicherweise 1 – 5 Stunden, die Abkühlung erfolgt werkstoffabhängig im Wasser- oder Salzwarmbad. Die Nitrierhärtetiefen betragen ca. 0,25 mm (je nach verwendetem Werkstoff). Die Behandlung erfolgt vorwiegend zum Verschleiß- und Korrosionsschutz. Der Prozess kann entweder im Salzbad (Salzbad-nitrocarburieren) als auch in Ammoniakgas (Gasnitrocarburierung) erfolgen, wobei aktuell der Trend zum Gasnitrocarburieren geht. #
Das Nitrieren weist eine Vielzahl von positiven Eigenschaften auf. Es ist auf fast alle Stähle anwendbar. Es führt zu einer harten Oberfläche bei weichem Kern. Der Werkstoff bleibt verzugsarm, da keine Gefügeumwandlung stattfindet. Die Dauerschwingfestigkeit wird erhöht, das Verschleiß- und Korrosionsverhalten verbessert. Die Behandlung von Schüttgut ist möglich, ebenso ein partielles Nitrieren. Außerdem kann eine Nachoxidation nach dem Nitrocarburieren zur weiteren Verbesserung der Korrosionsbeständigkeit beitragen. In Verbindung mit wartungsfreien iglidur® Gleitlagern, die durch ihre selbstschmierenden Eigenschaften im Trockenlauf, d.h. ohne externe Schmierung durch Fette oder Öle, betrieben werden können, sind beide Nitrierverfahren mit Blick auf einen niedrigen Verschleiß und Korrosionsschutz empfehlenswert.
Insgesamt gilt für Nitrit-behandelte Wellen, dass sie in der Regel ein signifikant besserer Gegenlaufpartner für iglidur® Werkstoffe sind, als das unbehandelte Ausgangsmaterial. Ein großer Vorteil im Vergleich mit verzinkten Oberflächen liegt darin, dass keine Schicht aufgetragen wird, sondern das eigentliche Wellenmaterial durch die Diffusion von Sticksto‑ bzw. Kohlenstoff verändert wird. Somit können auch oberflächliche Beschädigungen – in Abhängigkeit von der Diffusionstiefe – den Korrosionsschutz nicht reduzieren. Anschaulich werden die Unterschiede bei einem Vergleichstest.
Beide Lager wurden in der gleichen Maschine unter identischen Bedingungen (Schwenk-Anwendung, hohe Kräfte, Kantenlasten, Schmutz) eingesetzt. In beiden Fällen haben wir mit dem Gleitlagerwerkstoff iglidur® G getestet. Die verwendete ST52 Welle kam in identischer Ausführung mit galvanischer Verzinkung und gasnitriert zum Einsatz. Bei der verzinkten Variante wird deutlich: Im Bereich des Kontaktes zum Lager wurde die schützende Zinkschicht komplett abgetragen. Dadurch geht der Korrosionsschutz verloren. Es kommt zu einer massiven Korrosion der Welle. Die Folge ist ein massiver Anstieg des Reibwertes. Die Zerstörung des Lagers ist nicht auf Verschleiß im tribologischen Sinne zurückzuführen. Vielmehr ist das Material durch die Scherspannung förmlich zerrissen worden. Dieser Effekt konnte bei der nitrocarburierten Variante der Welle nicht beobachtet werden.
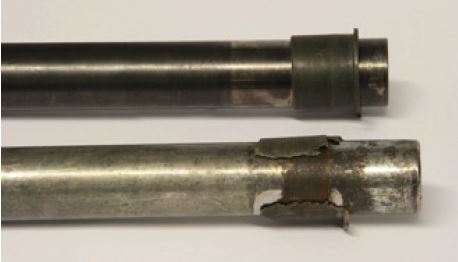
Wir beraten Sie gerne bei der Wahl der richtigen Kombination aus Welle und Gleitlager!
Sind Sie auf der Suche nach der passenden Welle für Ihre Gleitlager? Oder fehlt Ihnen gar beides? Haben Sie Fragen zu Beschichtungen von Wellen für Gleitlager? Wir unterstützen Sie bei der Auslegung ihres Gleitlagersystems und liefern alles aus einer Hand. Wir beraten Sie unverbindlich und kostenlos, digital oder telefonisch.