3D drucken statt fräsen – Verschleißteile aus Hochleistungspolymeren
igu-blog-adm | 20. Dezember 2018
Konstrukteure, Instandhalter oder Einkäufer stehen immer vor der Herausforderung, die technisch und ökonomisch beste Lösung für Ihr Produkt bzw. ihre Anwendung zu realisieren. Oftmals ist das übergeordnete Ziel, die Stillstandzeiten von Anlagen und Maschinen zu verringern, um so Kosten einzusparen. Neben den Kostenvorteilen geht es auch darum, möglichst schnell und unter serienreifen Bedingungen, Prototypen herzustellen – auch Klein- und Mittelserien sind realisierbar. Das richtige Material und die schnelle Verfügbarkeit von Bauteilen spielen bereits in dieser frühen Testphase eine entscheidende Rolle und bestimmen den Erfolg eines Projektes entscheidend mit. In den folgenden Abschnitten erfahrt ihr welche Bauteile im 3D Druck gefertigt werden können, wann es sinnvoll ist auf den 3D Druck zu setzen und wo die Kostenvorteile gegenüber anderen Fertigungsverfahren liegen.
Was genau ist unter Verschleißteilen zu verstehen? Und wo liegen die Unterschiede zwischen Standard- und High-Performance Materialien?
Verschleiß beschreibt vor allen Dingen den Verlust eines Materials von der Oberfläche eines Festkörpers, geschuldet durch das dynamische Zusammenwirken mit einem weiteren Körper. Oder um es noch einfacher zu beschreiben – überall wo Bauteile in einer Anwendung bewegt (rotierend, schwenkend, linear) werden, herrscht abrieb und somit eine Abnutzung des Materials.
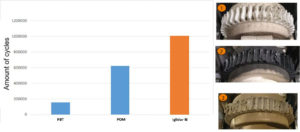
Verschleiß ist lästig und kostet Firmen viel Geld und deren Konstrukteure und Instandhalter eine Menge nerven – das geht auch anders! Dem Anschein nach, ist die Beschaffung von Maschinenbauteilen aus Standardkunststoffen oftmals die beste Lösung. Was aber, wenn ich mindestens einmal wöchentlich durch den hohen Verschleiß meine Maschinen und Anlagen zum Stillstand zwingen muss? Die günstige Beschaffung der Bauteile stehen in keinem Vergleich zu den Kosten eines Maschinenstillstands. Um Stillstandszeiten zu minimieren, eignen sich hochabrieb- und verschleißfeste Kunststoffe für Verschleißteile aller Art. Zum Beispiel für Gleitlager, Zahnräder oder auch Sonderverschleißteile, die bis zu 6 mal höhere Lebensdauer gegenüber gefrästen Standardmaterialien wie PBT (Polybutylenterephthalat) und POM (Polyoxymethylen) erreichen. Die Beschaffung war nie einfacher! Gedruckt statt gefräst. Mit dem 3D Druckservice sind Verschleißteile aus Kunststoff binnen 24 Stunden versandbereit. Wo wir gerade bei einfach sind: in nur zwei Schritten ist man beim fertigen Bauteil. Einfach per „Drag & Drop“ die Zeichnung als STP-Datei hochladen, zwischen verschleißfesten SLS- und FDM Materialien auswählen und in maximal 3 bis 5 Werktagen erhalten. Noch Fragen? Na dann nichts wie los und testen!
Wie hoch ist der Kostenvorteil gegenüber mechanisch bearbeiteten Bauteilen? Und ab wann lohnt es sich auf den 3D Druck zu setzen?
Angenommen wir beschäftigen uns mit einer Antriebsmutter in Sonder-Spindelgeometrie. Wir möchten diese aus einem Kunststoff-Halbzeug bzw. Platte mechanisch bearbeiten lassen. Das Werkzeug schlägt bereits mit mehr als 1000 Euro zu buche. Die Lieferzeit beträgt 3 Wochen. Im 3D Druck wird kein Werkzeug benötigt. Der Preis für Stückzahl 1 liegt bei 19 Euro und ist lieferbar ab 24 Stunden. So verhält es sich auch bei dem Schneckenrad. Bei einer mechanischen Bearbeitung fallen Werkzeugkosten von mehr als 5000 Euro an. Auch hier liegt die Lieferzeit bei über 3 Wochen. Das Gleiche Schneckenrad, mit dem Unterschied dass es 3D gedruckt wird, liegt ab Stückzahl 1 bei einem Preis von nur 50 Euro – versandbereit ist dieses auch wieder ab 24 Stunden. Übrigens, im 3D Druck lassen sich auch optimale Zahngeometrien herstellen, die mit spanender Fertigung kaum bis unmöglich zu fertigen sind.
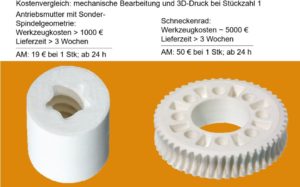
Ein weiters Erfolgsbeispiel für den Einsatz von 3D gedruckten Bauteilen ist die Antriebsmutter in Sondergröße (90 x 70 x 70 mm, BxHxT) für die Landstromversorgung von Schiffen. Um es kurz zu fassen: Schiffe die im Hafen anliegen sollen mit dem Stromnetz verbunden werden, statt die eigenen Motoren laufen zu lassen und so die Häfen zu verschmutzen. Der Bedarf liegt bei 3 Stück bei einer maximalen statischen Last von circa 12000 Newton. Die Herstellungszeit beträgt 48 Stunden. Weiterhin sind keine Nacharbeiten erforderlich. Kostenpunkt 307 Euro pro Stück.
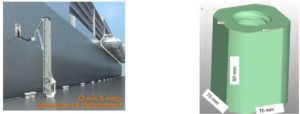
Wann setze ich nun welches Verfahren ein?
Am Beispiel einer iglidur Sonderbuchse spielen wir nun in Abhängigkeit der Stückzahl und des Volumens die einzelnen Verfahren durch.
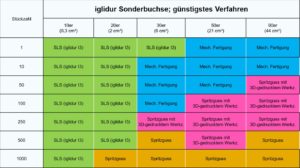
Der 3D Druck, insbesondere die Fertigung per SLS (Slektives Lasersintern) erweist sich dann als wirtschaftlich, wenn kleinere Bauteile (unter 5 g) benötigt werden. Merkt euch bitte weiterhin, je komplexer das Bauteil ist, desto mehr lohnt sich der 3D Druck im SLS – das gilt auch für Bauteile die mehr als 5 g aufweisen. Das Thema Präzision beschäftigt euch sicherlich noch bei den einzelnen Fertigungsverfahren. Als groben Richtwert könnt ihr euch im SLS-Bereich ± 0,1 Prozent merken. Sofern hohe Präzisionsanforderungen gewünscht sind, ist entweder eine Nacharbeit des gedruckten Bauteils oder die mechanische Fertigung aus Halbzeug die möglich.